UV Curing Lights – A Cure For What Ails You
As seen in: Auto Body Repair Network
It’s Time to Use UV Curing Products
With many shops across the country closed due to state shelter-in-place orders and many more worried about the fallout from what looks to be an impending, potentially severe recession, there’s no better time to look for new repair solutions for your business. In particular, these solutions should add revenue and cut waste, especially by allowing you to uptick throughput using fewer resources — namely, time and product costs.
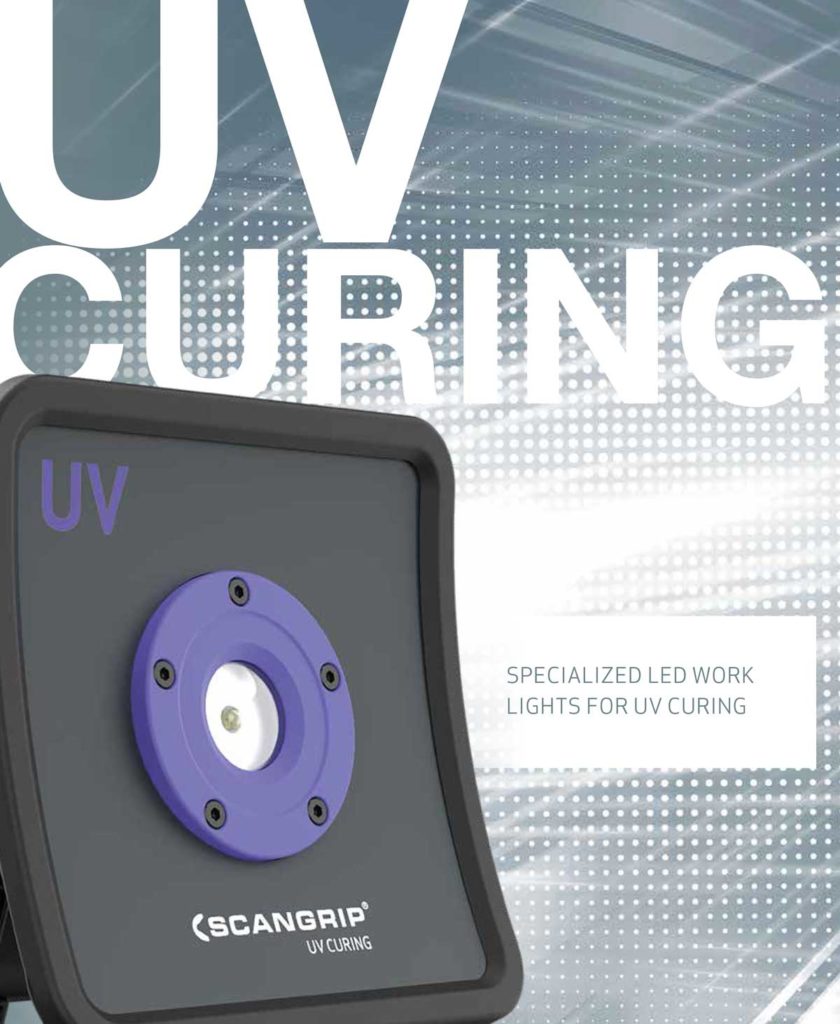
Innovative Tools is a US Distributor of the ScanGrip NOVA LED UV Curing Light. Learn more here
Let’s throw in one more cost you’ll want to reduce: utilities. UV-cured products check all these boxes and have the added benefit of being better for the environment, making your shop cleaner and safer for your employees and community. These products are engineered to work quickly at lower costs, which includes slashing your use of electricity and gas. They’ve also made a place (small, but growing) in collision repair.
So why have you and many of your colleagues waited so long to use them? According to Randy Drury, owner of Full Service Auto Stop in Houston, it’s usually because repairers either see them as still too new to the industry or are a bit wary of change. “You stick with what works,” says Drury. “Switching to waterbornes wasn’t that difficult for shops because you’re using a familiar finish basically the same way and with only a few changes. UV products challenge how you’ve worked before, and folks can see them as a bit too risky.”
Taking calculated risks is a key part of surviving and expanding in any business. Turning to newer technology — even during a business downturn and, perhaps, especially at such a time, could be a game-changing move. Here’s what you need to know about UV finish technology, the solutions, challenges and options available to your shop.
UV Curing Light Basics
Getting a firm, workable grasp on UV-curing technology begins with understanding how any finishes cure. Curing, in the world of automotive finishes, occurs when solvents in the finish vanish (evaporate) from any pigment, so that only a coating on the substrate remains. During this process, that remaining layer hardens. Ambient temperatures typically cause the solvent to dissipate. To speed along this process, heat is applied. Depending on the automotive finish and amount of heat supplied, curing can take anywhere from 30 minutes to 12 hours.
UV curing is a photochemical process created when high intensity, ultraviolet light is applied to coatings containing photoinitiators. Photoinitiators are molecules that release free radicals (atoms, molecules or ions with unpaired electron that make them highly chemical reactive). Photoinitiators essentially replace auto refinishing hardeners. When UV radiation is applied, the photoinitiators go to work building chains of molecules that create the final layer of coating at souped-up speeds. Basically, a special light is focused on a specialized finish for quick results.
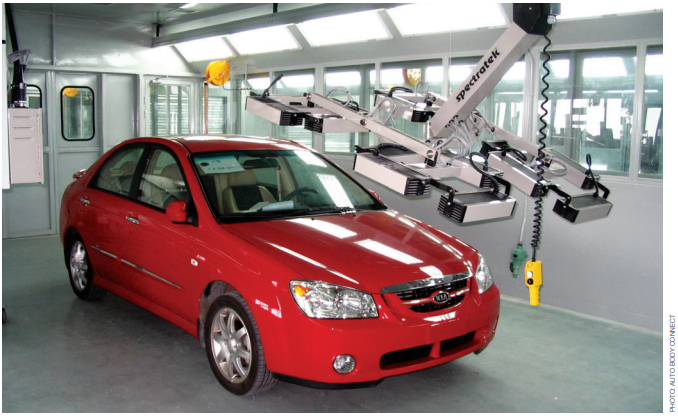
UV LAMPS ARE AVAILABLE FOR LARGER JOBS, but smaller versions like the ScanGrip NOVA UV Curing Light used for UV primers can provide significant savings in resources and labor for quick repairs.
OEMS have used UV technology for years to apply finishes and create other important chemical bonds in the factory. This technology has yet to realize its full use in collision repair due to costs, but has been evolving. AkzoNobel, for example, began offering a UV clearcoat 10 years ago.
UV products have also made their way into windshield and headlight repair. This article will focus on the most popular, growing area of UV technology, UV primers. UV primers are a particularly cost-effective use for this technology since their ability to greatly cut repair times lends itself to small repair jobs whose work time can be reduced from 30 minutes up to an hour instead to mere minutes. The handheld UV lights currently recommended for this work do typically cost around $2,000, which isn’t cheap, but they’re still very affordable in light of all the potential uses for this technology and considering the steep savings in energy and labor. The ScanGrip NOVA UV Cold Curing Light Starts at only $389. Learn More Here.
Putting UV Curing to Work in Your Collision Repair Shop
What can shops expect when using UV products? SATA, which creates a line of special guns dedicated to spraying UV primers, has created a number of videos on YouTube explaining the application process.
SATA notes that the application process for UV primers will differ from one manufacturer to another. There is a basic process. Painters apply the primer to the work area in thin layers. From there, the UV light is directed on the area, often from less than 12 inches away. The length of time the light needs to be applied also will vary based on product and size of the repair. SATA says a repair area the size of a volleyball frequently can be repaired in 30 seconds.
SATA says an additional benefit of using UV lights is the absence of heat, meaning a variety of substrates (including plastics) can be repaired. Also, a repair can be sanded or polished immediately after the light has done its job.
Mind the Challenges
While relatively simple, using UV technology does pose some challenges. Namely, you’ll need to stick to manufacturer guidelines both for the coating and the light. Keep in mind also that a number of factors can prevent a finish from curing properly.
One of the most common is failure to use the UV light for the necessary time. When this happens, the light doesn’t reach the photoinitiators at the finish’s deepest layers, preventing the finish from curing and causing what’s known as adhesion faults. In some cases, if sunlight hits the finish before or while it’s being sprayed (even for the finish on the tip of the gun), it can begin to harden too soon, creating more finish problems.
For these reasons, you’ll want to get some training for your UV products and make sure your painters/techs gain some experience before using them on paid work. Drury says his workers first tested this technology on practice panels to get a better “feel” for spraying and curing the finishes. “The learning curve isn’t steep. It shouldn’t scare off anyone,” he says. “But it’s necessary. In our case it also helped sell their [UV products] use to the staff.”
As with any repair products, use the proper personal protection equipment (PPE). Always cover all exposed skin, including hands and face, and wear UVrated eye protection.
Available UV Curing Light Filler Options
What products could be making a difference at your shop? Manufacturers suggest the following:
AkzoNobel UV Curing Body Filler
AkzoNobel says its Autosurfacer UV is one of the fastest-curing fillers and can be used for 85 percent of all repairs. The filler requires five minutes of UV-A exposure to fully cure, is isocyanate-free and can reduce paint usage up to 50 percent per job compared to conventional primers.
Other benefits include:
- Can be sanded in one step immediately after drying and it can be applied
directly to metal - Is a 1K product, making it easier to
use and reducing the risk of mixing
errors and waste - Does not require a wash primer on
steel surfaces - No pot life to deal with
BASF UV Repair Primer
BASF suggests its newest UV product, Glasurit 151-70 primer, available both in liquid and aerosol form. The primer is designed to be easy to use since it’s a 1K off ering and includes a self-guide coating to prevent tacky or sticky layers on the surface once cured and provides an exceptionally fast cure. BASF says Glasurit 151-170 UV Primers are 100 percent cured, means there’s no dieback or shrinkage in repair areas.
The primers promise drastic gains since they can cure in a matter of seconds instead of minutes. Visit www.basfrefinish.com to learn more.
PPG UV Auto Body Primer System
PPG’s OneChoice UV primer system now includes a handheld UV light, along with protective gloves and glasses. The company says technicians can complete spot refinish repairs in two to three minutes using its SUA1080 UV primer and SXA1081 UV primer cleaner. The SUA1080 UV primer is a “shake and spray” product requiring no mixing and is designed to be ready quickly after application after sanding, with no waste, no pot life issues and no need for spray gun cleaning. PPG says the light makes the curing process more effective and convenient compared to fixed-position lamps.
Other manufacturers have either started selling or begun looking at adding UV lights to their product offerings. All provide documentation specifying UV light models that can be used with their products.
Making the Case for A UV Curing Solution
This level of support makes for a quick transition from simply considering UV products to incorporating them fully into your services. If you’re sizing up revenue-boosting/cost-saving options, being able to fast track them to the shop floor is significant. Acting, while others are considering moves, is almost always a good strategy.
For some perspective, go back 12 years when the country slipped into a deep recession that tested the mettle of every shop, even the most successful. Today, those repairers reflect on lessons learned there to guide them when difficult times arise again. They adjusted their operations, cut costs, actively pursued business where they could find it and came out of the experience stronger, leaner and meaner.
For you now, this lesson could mean incorporating new technologies like UV and taking other smart risks that shine a transformative light on the need to change and adapt today and tomorrow.
Stay well.
Written by: TIM SRAMCIK // Contributing Editor with Auto Body Repair Network
About Innovative Tools
Innovative Tools and Technologies is dedicated to helping customers be more efficient, productive, and profitable.
Innovative's passions don't end there. With the creation of the Innovative Movement, we are saving shop classes and helping invest in the next generation of auto body technicians!